The Ultimate Guide to Dental Handpiece Maintenance
How best to look after the dental handpieces, maintain efficiency for longer and to increase the lifespan and ultimately reduce your outgoings.
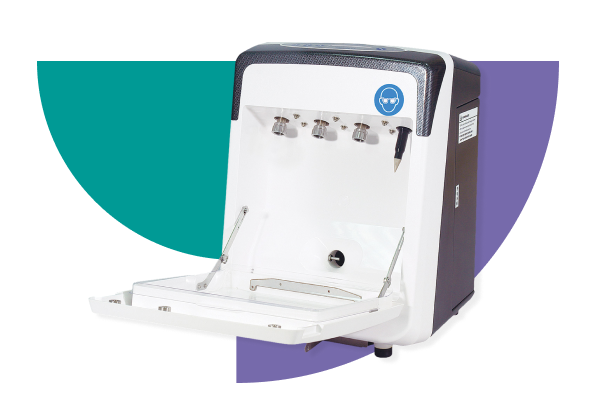
How best to look after the dental handpieces, maintain efficiency for longer and to increase the lifespan and ultimately reduce your outgoings.
Dental handpieces are not cheap. The costs of continually replacing and repairing turbines and contra angles can quickly mount up and put a big dent in a practice’s budget. With some basic understanding of how dental handpieces work and how best to look after them, handpieces can maintain efficiency for longer, have a greater lifespan and ultimately reduce your outgoings.
High speed turbines are dental handpieces powered by air. They remain the most widely used type of handpiece in dental practices. In these handpieces, the turbine is the only moving part. The turbine is made up of a set of two bearings, two O rings and a spindle/chuck. Situated in the head of the handpiece, the upper and lower bearings are supported beneath them by O-rings. These provide vibration and noise dampening.
A typical bearing is made up of an outer race and an inner race. The races create a track for the ball bearings to travel around in. A bearing retainer, also known as a cage, keeps the balls from banging into each other and keeps them straight and smooth. This is the key component in any handpiece and is what normally breaks and causes the handpiece to stop working properly. Any trapped debris in the bearings can cause the races and retainer to wear away and the rotation of the bur to get sloppier.
In the centre of the turbine head is a chuck which holds the dental bur. Wrapped around this is the bur tube, an outer sleeve that is supported by the two bearings at either end. Pressed onto the outside of the bur tube is the rotor. The rotor is what makes the bur tube spin when compressed air is applied.
Correct air pressure is critical to handpiece longevity for two reasons. The first relates to the precision bearings located inside the handpiece head which have a recommended pressure that should not be exceeded. Applying air pressure past these recommended limits will cause handpiece failure at a quicker rate. Handpiece repair companies will likely want to know your air pressure to see if it is set too high. Most dental units come pre-equipped with an air pressure gauge. These however are not always the most accurate at measuring pressure because they do not account for the loss of air pressure that occurs as air travels from dental unit to handpiece.
Gauges can be purchased that screw directly into the dental unit tubing and connect to the handpiece to provide an accurate, inline reading of air pressure. Most dental chair service engineers should be able to provide this. Most dental units have settings on them to allow the pressure of each individual handpiece line to be controlled. All handpieces manufacturers should be able to provide details of what this optimum pressure should be. If air pressure is too low, the handpiece will not be as efficient at cutting.
Dental handpieces should always be lubricated prior to autoclaving. Handpieces should be autoclaved after every use.
Oil should always go into the smaller of the two larger holes. This is a universal rule irrespective of manufacturer. This hole is the one which air is driven into. The bigger of the two large holes is the exhaust. Other holes on the handpiece are for the water coolant and fibre optics.
Aerosol is preferred for lubricating high speed handpieces as it allows the user to spray through the hole until they see oil coming out of the head. This provides quick confirmation that the oil has penetrated the bearings.
Droppers on the other hand rely on the air pressure to drive the oil into the bearings. It is important that the right nozzle is used for the handpiece being lubricated. Handpieces with swivel connectors or quick disconnectors have unique spray tips that lock tightly into the handpiece base when lubricating to force out any debris.
Excess oil should always be run out of the handpiece following lubrication. Failure to do this can cause oil remnants to bake and turn into a glue that sticks to the ball bearings when autoclaving.
Running out should also be done to avoid any oil accidentally being sprayed into a patient’s mouth.
This can be done by running the handpiece on the hose or with the using of a special flushing station.
If the handpiece is under warranty, then it is advisable to ensure you use dental handpiece oil belonging to the same brand/manufacturer as your handpieces so not to risk voiding any guarantee.
If the handpiece is not under warranty, then any universal lubrication spray for handpieces should suffice.
Investing in an automatic lubrication device, can provide the following advantages:
Price and counter space should be factored in when considering a purchase. Prices typically range between £1000 and £2000.
Other beneficial features to look out for are fully automatic operation and a chuck cleaning attachment like that seen on the BA Ultimate CL0 Lubrication Unit.
Autoclaves, also known as steam sterilisers, are self-sealing steel machines that use a combination of heat and time to kill microorganisms and make dental handpieces safe to use again. The three main classifications of autoclaves are S class autoclaves, B class autoclaves and N class autoclaves.
B class autoclaves are the most suitable machine for a dental practice in accordance with European Standard 13060. They remove air from inside the chamber by means of a vacuum pump, creating a negative pressure that forces steam in. They are generally capable of much faster sterilisation and drying cycles, enabling dental staff to work much more efficiently.
For more information on how different autoclaves work and what to consider when purchasing one, visit our Ultimate Guide to Autoclaves.
Unlike air driven handpieces that have only one moving part, electric handpieces have several. Because they are driven by an electric motor, electric handpieces have almost unlimited torque. This makes it harder for dentists to realise when the handpiece might be malfunctioning. This provides a greater risk of patient injury and therefore extra care is needed to make sure the handpiece is always working properly.
The following are some quick checks that can be carried out for a strong indication that your handpiece is working properly and does not need repair:
Electric motors, also known as micromotors, cannot turn as fast as air turbines. To power a high-speed handpiece, gears are needed to increase the speed of an electric motor, often by a ratio of 1:5. Electric handpieces are also called speed-increasing handpieces, working at cutting speeds over 180,000 revolutions per minute (rpm). With a 1:5 handpiece, if the motor is turning at 40,000rpm the bur will be turning at 200,000 rpm.
The process of lubricating high speed electric handpieces and contra angles is very similar to that of turbines. An appropriate nozzle should be applied and the oil should be sprayed through the handpiece until it flows out of the head to ensure penetration of all necessary internal components. With low-speed handpieces that reach speeds of only 5,000 rpm, not as much oil is required. Droppers are often preferred for low-speed handpieces as too much oil can cause the handpiece to become sluggish. As with turbines, oil should be put into the smaller of the two large holes.
DIY options available when your handpiece breaks include purchasing a new turbine from the handpiece manufacturer or rebuilding the turbine entirely. Doing this can easily backfire and end up costing a lot more money. Often the best and safest option available is to send the handpiece back to its manufacturer for the best possible repair. In partnership with B.A. International, Kent Express provides a fast handpiece and small equipment repair service. The standard turnaround for handpieces is 24 hours, with in-depth fault diagnostics, experienced technicians and restoration to specification using premium ceramic bearings.
For help with your handpiece maintenance or repairs, speak to Jack our handpiece specialist on 01634 878759.
For help with your handpiece maintenance or repairs, speak to Jack our handpiece specialist on 01634 878759.
For help with your handpiece maintenance or repairs, speak to Jack our handpiece specialist on 01634 878759.